Foamed Bitumen
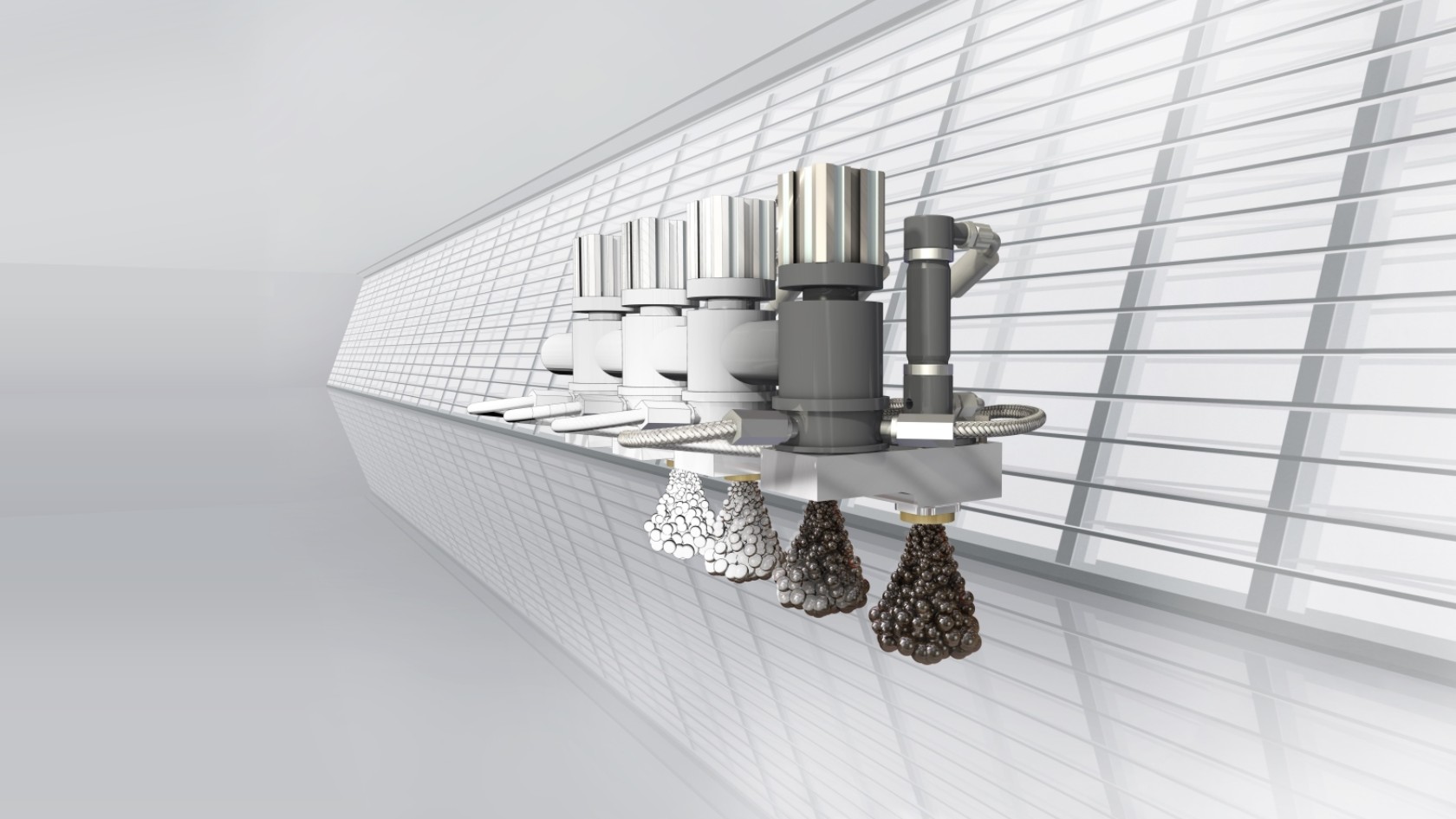
Cold recycling using foamed bitumen as a binding agent is an established technology worldwide and is increasingly becoming the focus of road authorities and construction companies for the rehabilitation and new construction of roads. Cold recycling with foamed bitumen makes it possible to produce flexible and long-lasting base layers. These create the perfect foundation for the final asphalt layer with reduced thickness. Foamed bitumen is produced from normal bitumen at a temperature of approx. 175°C using state-of-the-art technology. Inside WIRTGEN recyclers, microprocessor-controlled injection systems precisely produce and inject the foamed bitumen into the aggregate.
In numerous countries around the globe, well over 100 million square meters have already been recycled with foamed bitumen!
Foamed bitumen is derived from the process of “foaming” the bitumen – this involves injecting a small amount of water and air under high pressure into heated bitumen, which foams and expands to 20 times its original volume. The foam is then added directly to the mixer via injection nozzles and thoroughly blended into cold and moist aggregates. The new building material – often produced using reclaimed asphalt pavement – is then referred to as BSM (bitumen-stabilized material).
The foamed bitumen quality can be precisely defined in the laboratory prior to the start of construction by carrying out preliminary tests using the WLB 10 S mobile laboratory unit. Parameters such as water quantity, air pressure, and temperature can be varied quickly thanks to its simple operation. The quality of the foamed bitumen is primarily defined on the basis of the parameters “expansion” and “half-life.” With the WLB 10 S mobile foamed bitumen laboratory unit and the WLM 30 twin-shaft pugmill, we have translated our many years of application experience into state-of-the-art laboratory technology. Using our state-of-the-art machines, suitable test specimens can be produced in no time at all.
It’s All about the Mix
WIRTGEN’s WLB 10 S foamed bitumen laboratory unit performs the following tasks:
The WLB 10 S can be connected directly to the WLM 30 twin-shaft pugmill for mix production in the road construction laboratory. The foamed bitumen produced by the WLB 10 S is then injected into the mixing process in the WLM 30. The materials are mixed precisely and without any losses. This process produces mixes for the production of test specimens in no time at all.
The ability to be processed easily is one of the distinguishing features of BSM mixes. As long as it is kept sufficiently moist, subsequent compaction measures do not need to be carried out in any specified period time. Yet another very important hallmark of BSM layers is that they can be opened to traffic temporarily immediately after completion. The cold recycled layer is often simply covered with a thin asphalt surface that serves as a wearing layer. The focus of the maintenance work is also only on the asphalt surface layer, while the cold recycled layer remains unaffected. This, in turn, translates into low road maintenance costs.
Material Structure
Cold mixes produced with foamed bitumen behave like building materials with constant inter-particle friction but with a significant increase in cohesion and strength. This material is also known as BSM (bitumen-stabilized material). With BSM mixes, the aggregate is not coated, but instead the bitumen is mixed homogeneously – usually 1.5% to 2.5% of the building material mix by mass. After final compaction, the material is characterized by excellent flexibility and high bearing capacity. It has a proven track record around the globe. Material treated with foamed bitumen is characterized by its excellent strength and bearing capacity.
In-Situ Cold Recycling
Cold recycling with foamed bitumen can either be carried out in-situ (i.e. on site) or in-plant (i.e. in a plant). During in-situ cold recycling, a cold recycler granulates the damaged pavement and homogeneously mixes in foamed bitumen as well as cement and water as required. This produces a new bitumen-stabilized mixture (BSM) in a single operation. The cold recyclers designed for in-situ processing are equipped with an efficient milling and mixing rotor as well as an injection system. Some machine models are also equipped with a screed for paving and precompaction of the new BSM mix.
In-Situ Materials
In principle, all unbound building materials – as well as reclaimed asphalt pavement – can be processed using foamed bitumen. WIRTGEN recyclers granulate both the asphalt layer and the underlying layer and then mix the material with foamed bitumen in-situ in a single operation. The result is a high-quality bituminous base layer that, after compaction, is capable of withstanding extremely high traffic loads.
In-Plant Cold Recycling
During in-plant cold recycling, removed road pavement is transported to the mobile cold mixing plant near the job site. Here the milled material is homogeneously processed together with foamed bitumen and, if required, additional cement and water to form a new cold (BSM) mix that is ready for immediate paving. It can then either be immediately paved true to line and level or stockpiled for later paving.
State-Of-The-Art Injection System
The thermostat-controlled heating system ensures that the entire injection system operates at the ideal temperature before and during foamed bitumen production for outstanding quality – guaranteed. This eliminates the need to flush the system in a time-consuming process in event of an interruption or when on-site operations are ending. A microprocessor controls the foaming process and the quantities added.
In-Plant Milled Material
The milled material produced by WIRTGEN cold milling machines can usually be processed immediately after extraction or stockpiled for a long period of time. WIRTGEN’s KMA 220 mobile cold mixing plant produces in-plant cold mix from this raw material for subsequent paving with a VÖGELE asphalt paver.
Recovered and New Materials
Materials recovered from existing pavements, recycling materials, and new materials are processed using appropriate crushing and screening technology and are subsequently mixed with foamed bitumen in the KMA 220 cold mixing plant. Any road construction material with a suitable particle size distribution can be processed with foamed bitumen.
Low Total Costs
Due to the low amount of binding agent required, the ability to reuse RAP, and the significant time savings, these construction methods are particularly cost-effective with respect to manufacturing costs. In addition, by reducing the thickness of the asphalt superstructure, total costs are significantly reduced. But the cost of maintenance is also extremely low. This is because BSM layers do not tend to crack as a result of aging as is common with ordinary asphalt layers. The major advantage of this is that if rehabilitation is necessary, only the upper, thin asphalt surfacing needs to be renewed – eliminating the need to replace the entire asphalt pavement in a cost-intensive process. Due to its superior design and exceptional material properties, BSM is also increasingly being used in public-private partnership (PPP) projects.
Fully Recyclable
Due to its numerous benefits, foamed bitumen holds the top spot among binding agents. Asphalt granulate can be fully recycled together with foamed bitumen, regardless of whether it is cold or not. Processing without heating the raw materials offers tremendous CO2 savings potential. Small additive quantities of only 1.5% to 2.5% of total mass result in only marginal costs. Road bitumen is used all over the world and can be used immediately without additional preparation. Material mixed with foamed bitumen can be immediately paved, compacted, and opened to traffic, keeping construction times and traffic disruptions to a minimum.
Green Road Rehabilitation
Economic efficiency and environmental protection are not mutually exclusive – resource-saving foamed bitumen technology in combination with environmentally friendly WIRTGEN machine technology proves the validity of this statement. The process only uses recycled material with added binding agents. In addition, in contrast to construction using entirely new material, there is no need for environmentally unfriendly truck transports.